Der eine oder andere von euch hat ihn vielleicht schon auf Instagram oder TikTok gesehen, inzwischen ist auch mein Wagen 901-211 fertig. Die beiden fertigen Wagen seht ihr im Titelbild (901-212 links und 901-211 rechts)
Vorangegangene Artikel zum den Wagen findet ihr hier:
Die Wagen 901-211 und 214 waren ursprünglich nicht geplant, aber da der Unterschied zum geplanten 212 oder 213 hauptsächlich in der Seitenwand besteht und ich die anderen schon auf Basis der Zeichnung vom 211er konstruiert hatte, hatte ich die 3D-Druckdateien erzeugt und dann selbst auch genutzt.
Die Vielzahl der Seitenfenster nötigten mir Respekt ab, ich wollte diese diesmal nicht wie beim 901-212 und 213 aus einer alten CD-Hülle ausschneiden, zurecht feilen und einkleben. Daher habe ich einen Prototyp für eine komplette Fensterseite – also einen Sockel mit den 10 Seitenfenstern – gedruckt. Nach dem geglätteten der Oberseite – da könnte man noch viel mehr glätten – wurde eine Silikonform erzeugt und der Fensterblock mit einem klaren Resin gegossen. Wenn man es schafft, halbwegs blasenfrei und staubfrei zu arbeiten, kann man den Guss von beiden Seiten schleifen und am Ende polieren.
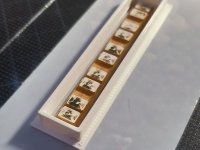
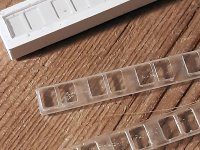
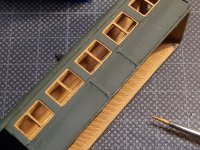
Für das verwendete Resin würde ich keine wirkliche Empfehlung geben, da meins bei exakter Mischung mehrere Tage braucht, um auf die nötige Härte zu kommen. Die Klarheit der Fenster ist für den Zweck brauchbar, aber deutlich niedriger als bei der CD-Hüllen-Version. Daher habe ich mich diesmal gegen Reisende entschieden.
Der Sockel der Fenster – wenn man ihn mitgießt und belässt – beansprucht etwas Raum, den ich vom gedruckten Innenleben abgefeilt habe, eine gesonderte Druckdatei gibt es dafür nicht.
Die einzelnen Fensterpaare passen, aber die gesamte Front ließ sich schlecht in einem Stück einsetzen, daher habe ich den Block unterteilt und die Fenster paarweise mit einem schnelleren Resin eingeklebt. Ich denke eine kleine Verschiebung der Maße hat sich beim Umweg über die Silikonform eingeschlichen.
Das Geländer der Plattform ist wieder aus Messingblech und -draht gebaut, die Kurbel – aus einem gebogenen Messingdraht in einem doppelt durchbohrten Blech (Bilder der Rohlinge hier drunter) – habe ich diesmal direkt angelötet, indem ich mit Klemmpinzetten eine Wärmeableitung erzeugt habe, so dass die Erwärmung durch den Lötkolben örtlich sehr begrenzt blieb. Für mich funktioniert das Verfahren zwischen die beiden Geländeteile den Übergang zu löten und dann Drähte für die Verbindung zum Dach durch selbiges zu fädeln bis gut, solange die "Möbel" und damit der Wagenkasten gut ausgerichtet sind.
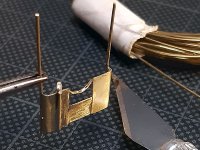
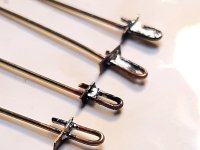
Zum Erreichen einer guten Kurvengängigkeit habe ich die Kupplungen nicht in Kupplungskästen mit Federn, sondern wieder mit einer Schraube unter dem Wagenboden angebracht. Möglich wäre auch eine feste Verbindung der Wagen als Zug. Angepasste Druckdateien für M2- und M3-Schrauben liegen inzwischen auch bereit … auch wenn ich M2,5-Schrauben verwendet habe ...
Alles was an 3D-Druckdateien zu den Wagen verwendet wurde und mir sinnvoll erschien, findet man für nichtkommerzielle Nutzung kostenfrei hier auf Thingiverse also viel Spaß damit.
Nebenbei, das Oberteil eines Wismarer Schienenbus für 1000mm Spurweite gibt es dort auch schon. Noch ist der nicht fertig gebaut, so dass ich ihn hier noch nicht vorgestellt habe, es fehlen noch Leitern, Gepäckgitter und eine Verblendung des Antriebs.
Update 2023-03-19
Inzwischen gibt es eine verbesserte Variante des 901-211 in TTm und H0m für den Resindrucker. Dabei sind Unterbau mit Innenraumausstattung und der Wagenkasten jeweils eine Baugruppe. Die Geländer und Übergänge der Plattform sind separat, um den Ärger mit abgebrochenen Teilen zu reduzieren. Bei der Gelegenheit wurden auch Niete und Verstärkungsbleche angedeutet, die Bremsen und Trittbretter überarbeitet. Zu finden ist das bei Printables (DE) und Thingiverse (EN).
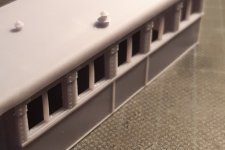
Vorangegangene Artikel zum den Wagen findet ihr hier:
Die Wagen 901-211 und 214 waren ursprünglich nicht geplant, aber da der Unterschied zum geplanten 212 oder 213 hauptsächlich in der Seitenwand besteht und ich die anderen schon auf Basis der Zeichnung vom 211er konstruiert hatte, hatte ich die 3D-Druckdateien erzeugt und dann selbst auch genutzt.
Die Vielzahl der Seitenfenster nötigten mir Respekt ab, ich wollte diese diesmal nicht wie beim 901-212 und 213 aus einer alten CD-Hülle ausschneiden, zurecht feilen und einkleben. Daher habe ich einen Prototyp für eine komplette Fensterseite – also einen Sockel mit den 10 Seitenfenstern – gedruckt. Nach dem geglätteten der Oberseite – da könnte man noch viel mehr glätten – wurde eine Silikonform erzeugt und der Fensterblock mit einem klaren Resin gegossen. Wenn man es schafft, halbwegs blasenfrei und staubfrei zu arbeiten, kann man den Guss von beiden Seiten schleifen und am Ende polieren.
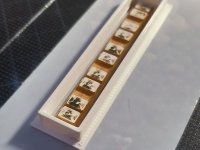
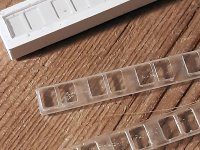
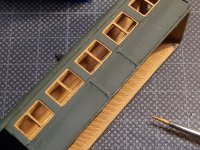
Für das verwendete Resin würde ich keine wirkliche Empfehlung geben, da meins bei exakter Mischung mehrere Tage braucht, um auf die nötige Härte zu kommen. Die Klarheit der Fenster ist für den Zweck brauchbar, aber deutlich niedriger als bei der CD-Hüllen-Version. Daher habe ich mich diesmal gegen Reisende entschieden.
Der Sockel der Fenster – wenn man ihn mitgießt und belässt – beansprucht etwas Raum, den ich vom gedruckten Innenleben abgefeilt habe, eine gesonderte Druckdatei gibt es dafür nicht.
Die einzelnen Fensterpaare passen, aber die gesamte Front ließ sich schlecht in einem Stück einsetzen, daher habe ich den Block unterteilt und die Fenster paarweise mit einem schnelleren Resin eingeklebt. Ich denke eine kleine Verschiebung der Maße hat sich beim Umweg über die Silikonform eingeschlichen.
Das Geländer der Plattform ist wieder aus Messingblech und -draht gebaut, die Kurbel – aus einem gebogenen Messingdraht in einem doppelt durchbohrten Blech (Bilder der Rohlinge hier drunter) – habe ich diesmal direkt angelötet, indem ich mit Klemmpinzetten eine Wärmeableitung erzeugt habe, so dass die Erwärmung durch den Lötkolben örtlich sehr begrenzt blieb. Für mich funktioniert das Verfahren zwischen die beiden Geländeteile den Übergang zu löten und dann Drähte für die Verbindung zum Dach durch selbiges zu fädeln bis gut, solange die "Möbel" und damit der Wagenkasten gut ausgerichtet sind.
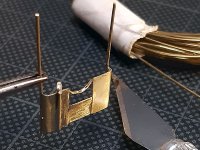
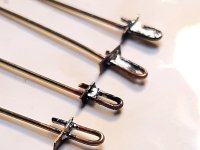
Zum Erreichen einer guten Kurvengängigkeit habe ich die Kupplungen nicht in Kupplungskästen mit Federn, sondern wieder mit einer Schraube unter dem Wagenboden angebracht. Möglich wäre auch eine feste Verbindung der Wagen als Zug. Angepasste Druckdateien für M2- und M3-Schrauben liegen inzwischen auch bereit … auch wenn ich M2,5-Schrauben verwendet habe ...
Alles was an 3D-Druckdateien zu den Wagen verwendet wurde und mir sinnvoll erschien, findet man für nichtkommerzielle Nutzung kostenfrei hier auf Thingiverse also viel Spaß damit.
Nebenbei, das Oberteil eines Wismarer Schienenbus für 1000mm Spurweite gibt es dort auch schon. Noch ist der nicht fertig gebaut, so dass ich ihn hier noch nicht vorgestellt habe, es fehlen noch Leitern, Gepäckgitter und eine Verblendung des Antriebs.
Update 2023-03-19
Inzwischen gibt es eine verbesserte Variante des 901-211 in TTm und H0m für den Resindrucker. Dabei sind Unterbau mit Innenraumausstattung und der Wagenkasten jeweils eine Baugruppe. Die Geländer und Übergänge der Plattform sind separat, um den Ärger mit abgebrochenen Teilen zu reduzieren. Bei der Gelegenheit wurden auch Niete und Verstärkungsbleche angedeutet, die Bremsen und Trittbretter überarbeitet. Zu finden ist das bei Printables (DE) und Thingiverse (EN).
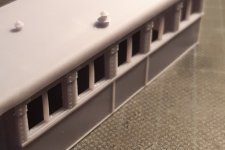